Morii Presents You World Class Aluminum Processing Technology for OPTICAL SYSTEM and MEDICAL Parts.
Morii Manufacturing is strong in the machining of aluminum precision parts and optical parts using lathes and multitasking machines.
We specialize in precision aluminum parts, optical parts, and medical parts made with lathes and multitasking machines.
We are a company that specializes in aluminum precision parts, optical parts, and medical parts made with lathes and multitasking machines.
We have a wide range of experience in optical and medical parts, from aluminum precision parts to machining of difficult-to-machine materials such as SUS and titanium.
We have a wide range of experience in machining difficult-to-machine materials such as SUS and titanium, and can handle everything from prototyping to mass production.
We can handle everything from prototyping to mass production.
In addition to aluminum thin-wall parts, we also accept orders for high-precision machining of copper, stainless steel, and other materials.
We also accept orders for high-precision machining of copper, stainless steel, and other materials in addition to aluminum thin-wall products.
Our products range from electronic parts to valves and fittings.
We can respond to a wide range of orders.
Our production system is fully prepared in cooperation with five partner companies.
Features of Processing Technologies
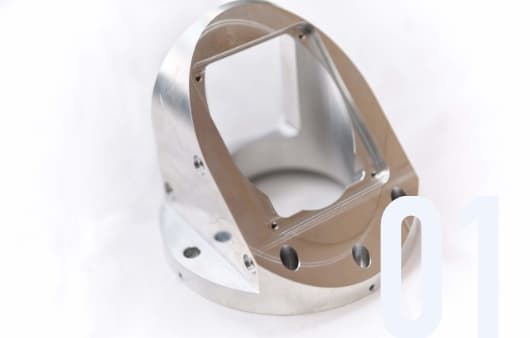
Strong in precision parts by multitasking machines, machining centers, and NC lathes
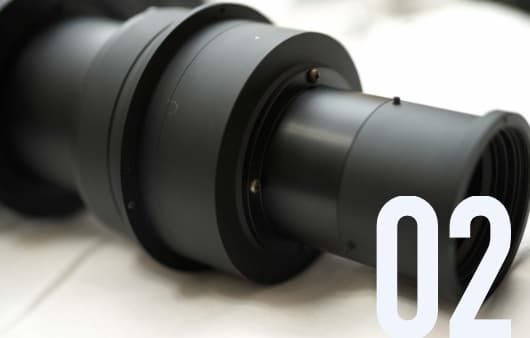
Coaxial, concentric, and multi-axial machining of zoom lenses, etc., which are common in optical components
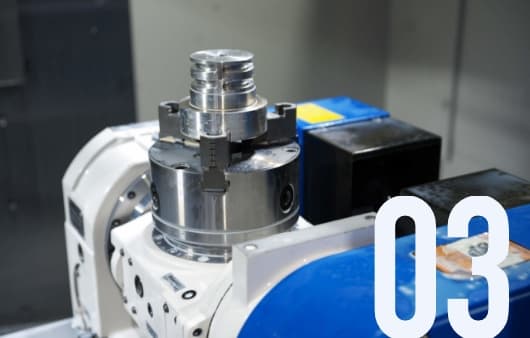
5-axis machining using a machining center and tilting NC circular table
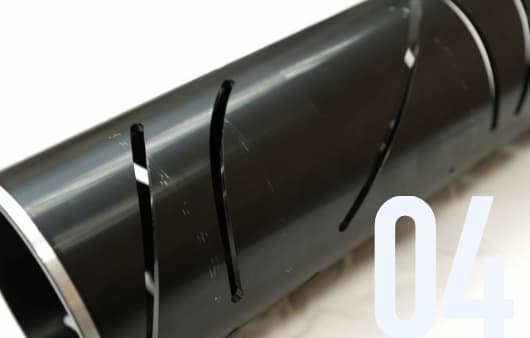
Long processing with thin-walled pipe
Track record: Machining φ118φ108330L inner and outer diameters without joints
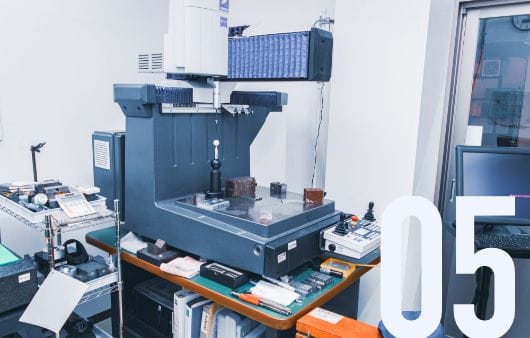
Normal products are inspected in the inspection room, while high-precision parts are inspected in the 3D Measuring Instrument Room.
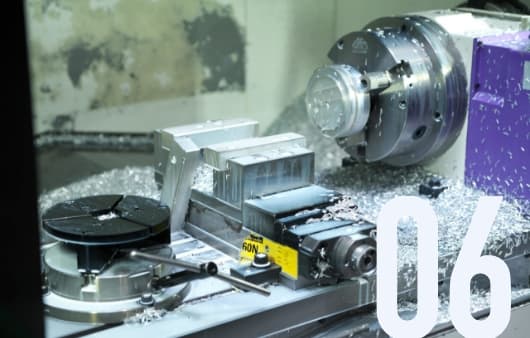
Cost reduction through efficiency gains by simultaneous machining (using a multitasking machine) and segregated machining (using both a multitasking machine and a machining center)
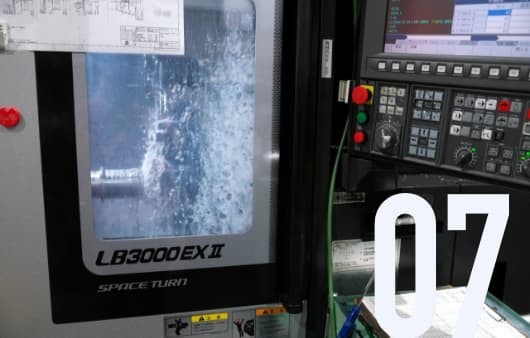
Balanced cutting using upper and lower turrets (to ensure accuracy)
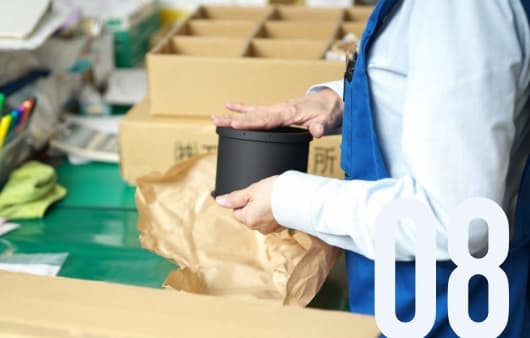
Integrated production from materials, heat treatment, polishing, and surface treatment is possible in solidarity with outsourcing
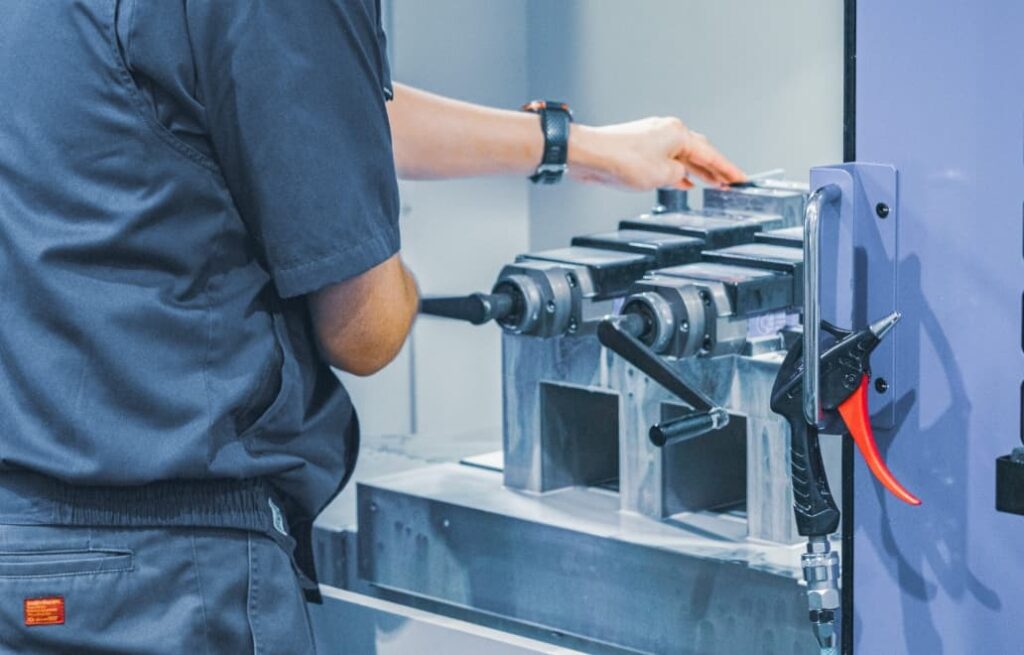
Technology
Each manufacturer’s machine performance is improving day by day in terms of accuracy, performance, and ease of use. However, it is still “people” who master the machines.
At MORII, each individual has the ability to meet high-level requirements, such as high-precision machining and applied machining technology.
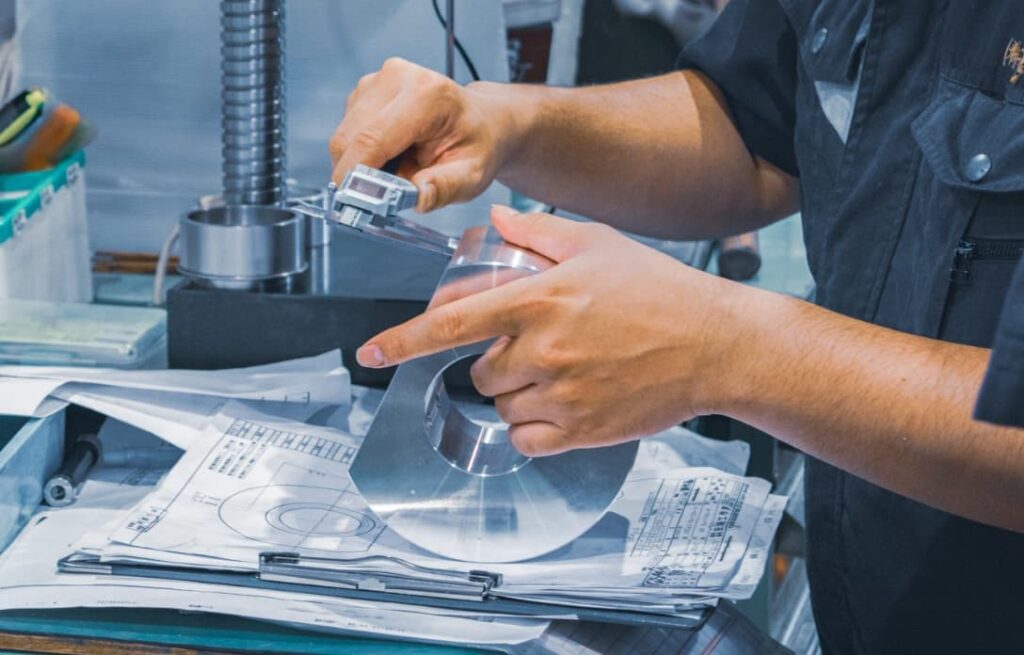
Quality
Ltd. has a strong track record in the machining of many optical components, especially aluminum materials, which are extremely difficult to handle.
In addition to aluminum, we also process and deliver iron, copper, titanium, and other difficult-to-machine materials with consistent high quality and high precision.
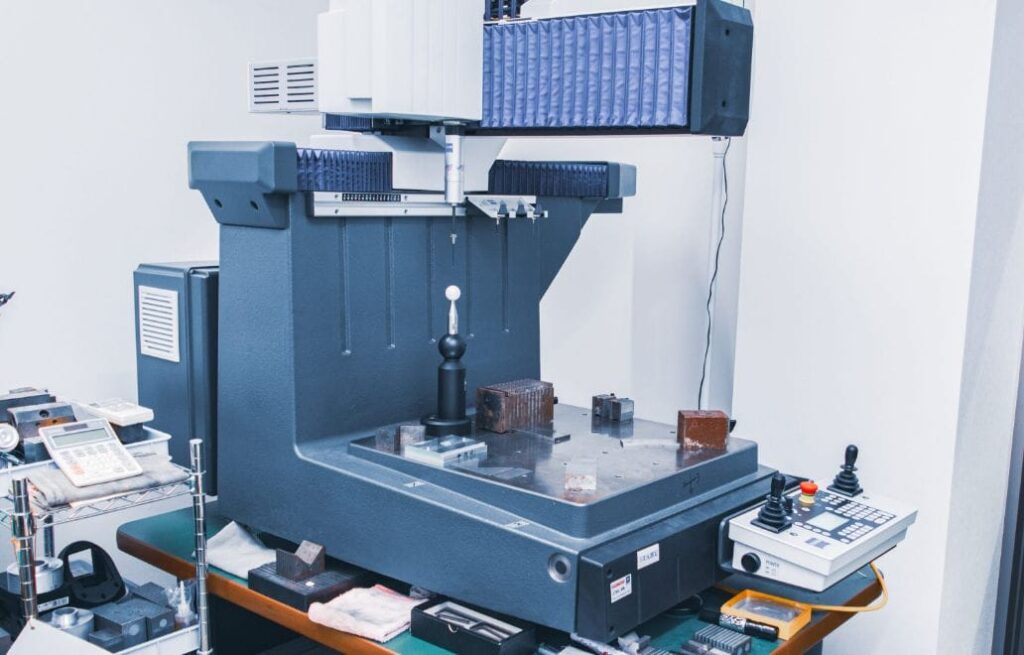
Examination
In addition to the normal inspection process, Morii Seisakusho Co., Ltd. has a dedicated inspection room where strict inspections are conducted.
Normal products are inspected in the inspection room, while high-precision parts are inspected in the 3D measuring instrument room.
By separating the inspection process, we are able to respond to all kinds of requests from our customers.
Key Points of Composite Processing
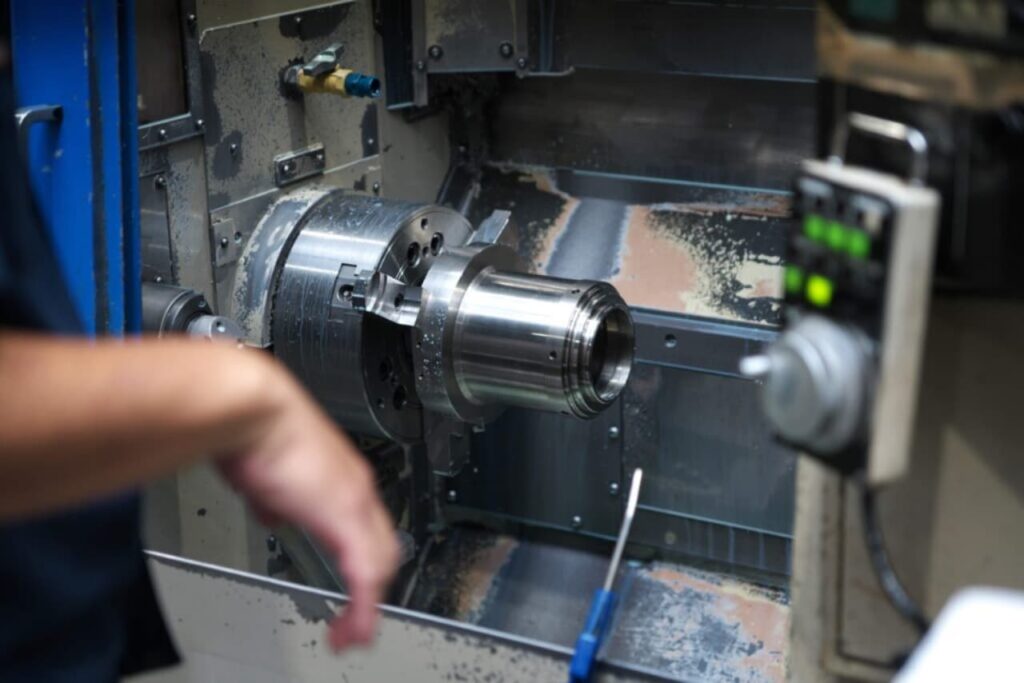
High-precision coaxial, concentric, multi-axis, and milling machining in a single chuck
MORII’s multitasking machining is characterized by its ability to perform coaxial, concentric, multi-axis, and milling machining with high precision in a single chuck.
The single-chuck machining process is ideal for optical parts that require high accuracy and a scratch-free appearance.
This is one of the reasons why Mory Mfg. has a large track record in optical parts.
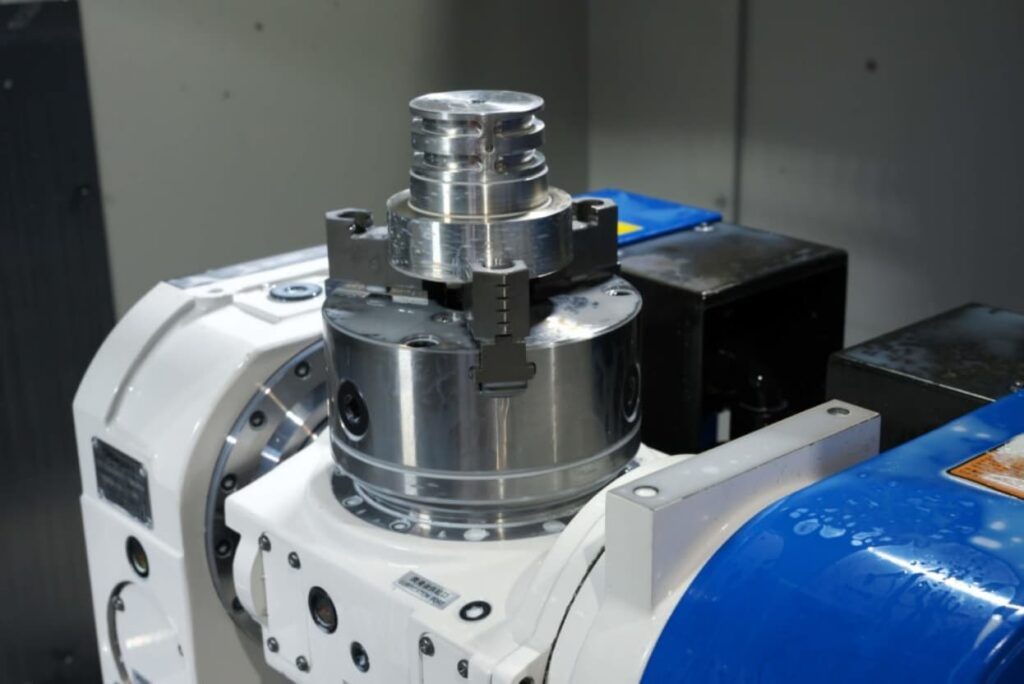
Selecting the right machine for the machining process rather than relying solely on multifunctional machining
If all machining is done on a multitasking machine, you may have the image that costs can be easily reduced because machining can be done only on the multitasking machine up to the final process.
Of course, there are parts that can be machined on a multitasking machine, but in fact, depending on the contents and number of parts to be machined, it may be much faster to use a separate machine, such as a machining center, for the milling process.
This is based on the past experience of Morii Seisakusho, and we can achieve optimum cost performance by identifying not only wasted processes but also wasted time.
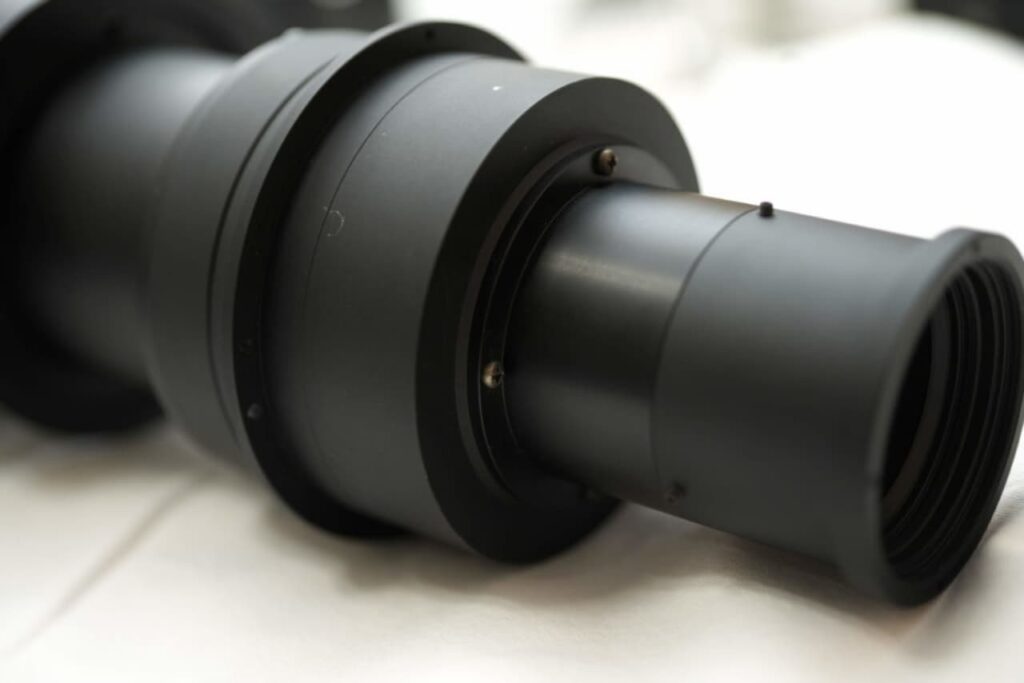
Seamless and beautiful processing of long and thin-walled pipes, both inside and outside diameters
Originally, not only multitasking machines but also NC lathes are not good at machining long and thin-walled pipes.
When machining from both sides, coaxial accuracy is reduced, steps are formed, and the appearance of the product is not very good.
However, Morii Seisakusho uses special tools to process both long and thin-walled pipes seamlessly and cleanly, both inside and outside diameters.
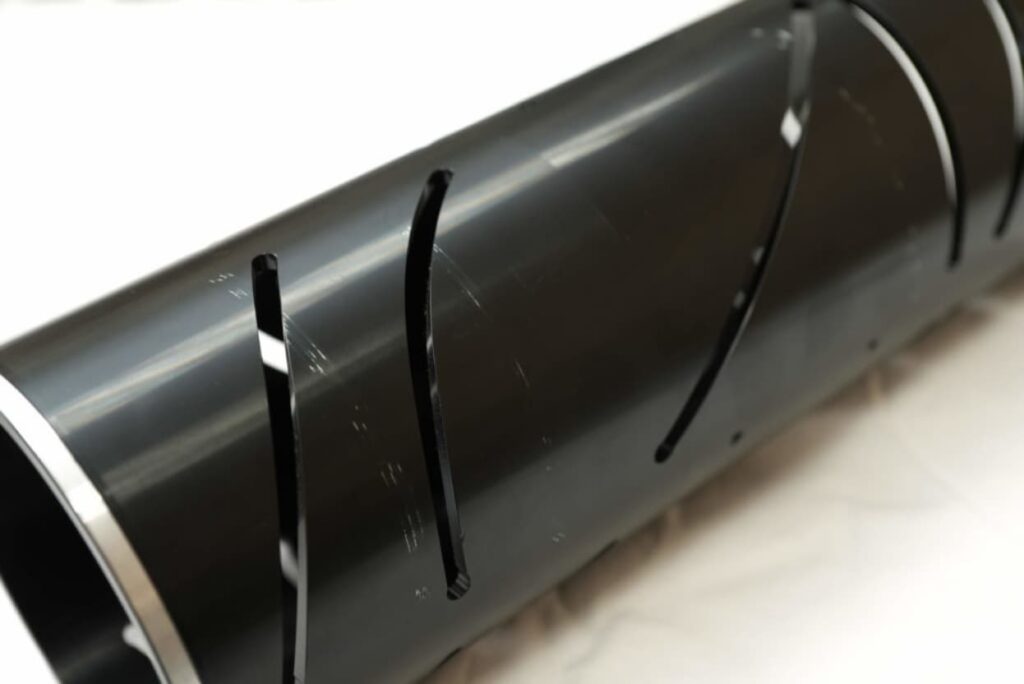
High-precision machining with minimal variation due to machining distortion and thermal expansion
The one-chuck process of composite machining also has a drawback: machining distortion.
However, it is not enough to solve only processing distortion; there is also the problem of expansion due to temperature.
Aluminum, in particular, has a large coefficient of expansion, so it is not possible to achieve the required accuracy if machining is carried out in a single-chuck process.
Of course, the same applies even if distortion is minimized by separating the processes instead of using a single chuck. Seasonal changes in temperature and the room temperature in the factory make it easy for variations in accuracy to occur.
However, at Morii Seisakusho, it is possible to process with sufficient machine precision and process control, while also taking expansion due to temperature into consideration.
Case Studies
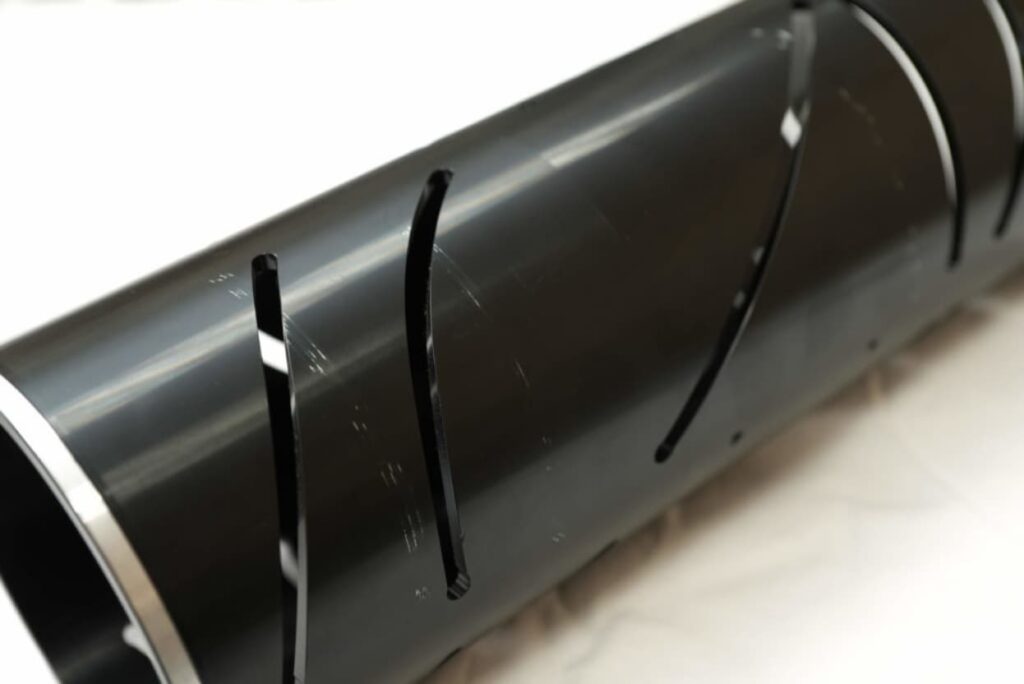
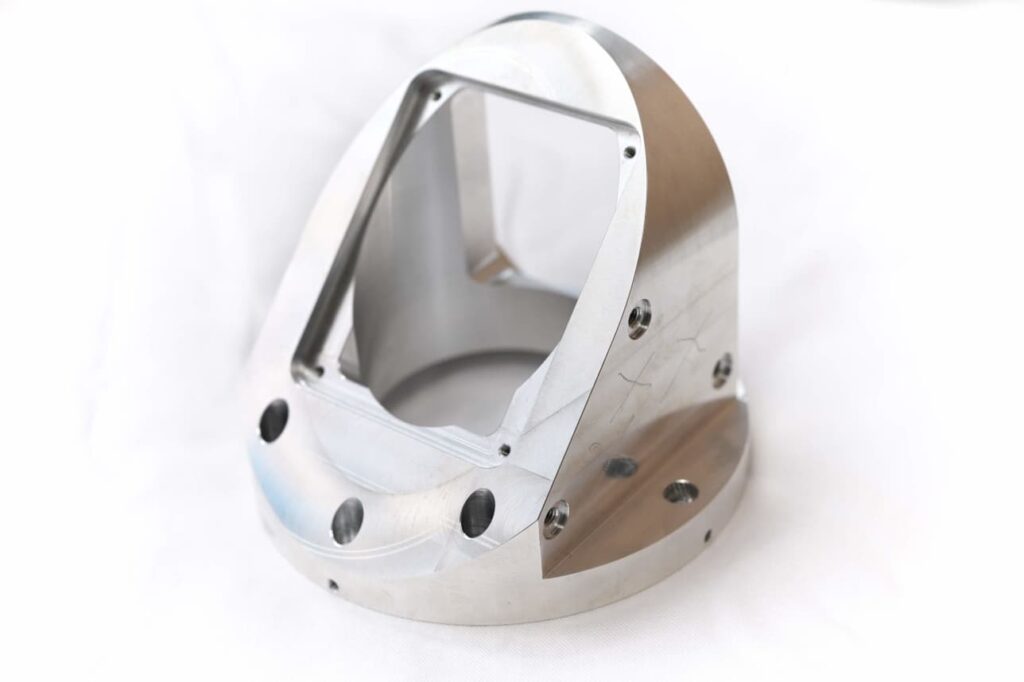
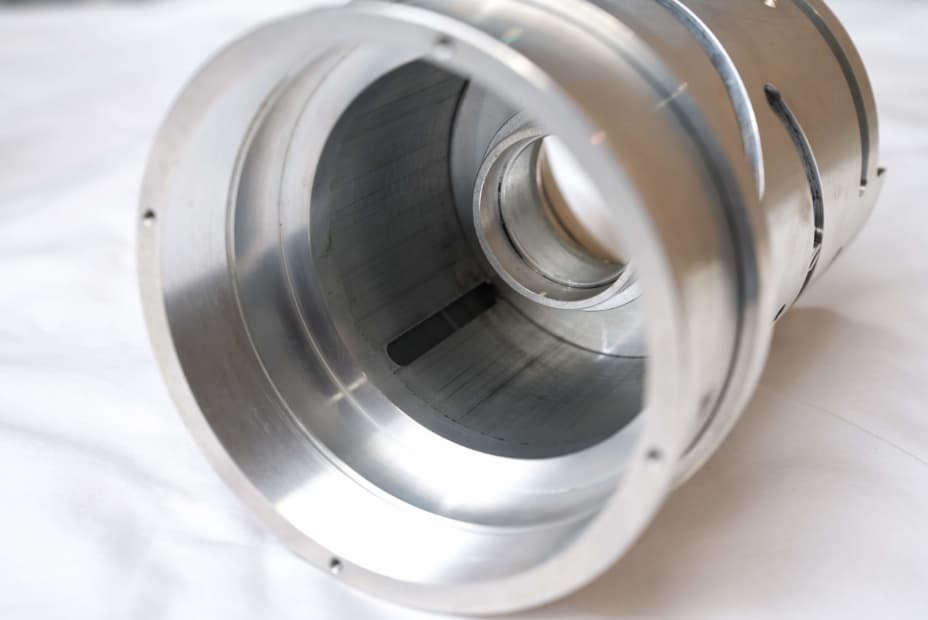
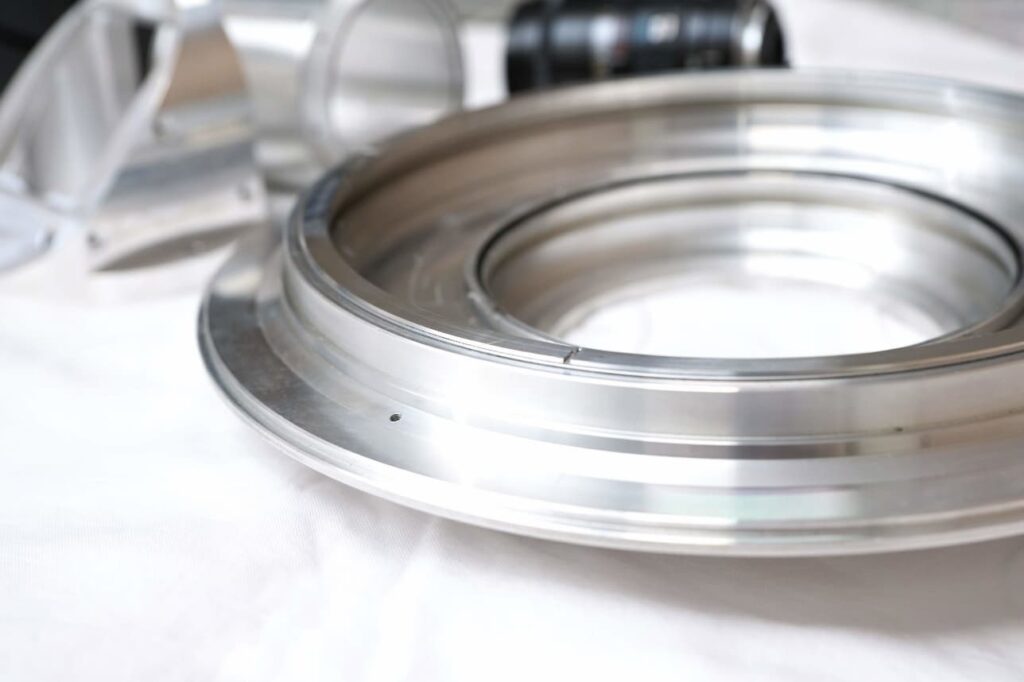
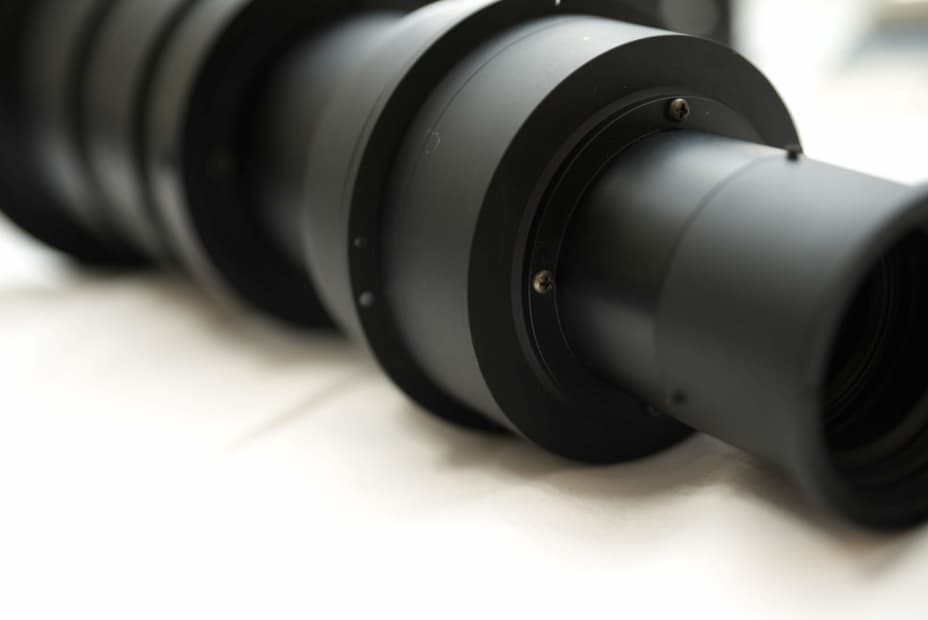
Frequently Asked Questions
- What is the maximum and minimum length of round material that can be processed?
-
Maximum φ300 x 700L Minimum φ0.5 x 2.0L
However, it depends on the shape and material, such as whether there is step processing, how deep the inside diameter is, and how thick the wall is. We also have a wealth of experience in forming blades that other companies cannot produce, and in long, thin-walled products.
- What is the outside diameter and length that can be processed by the multifunction machine?
-
The maximum size is about φ300 x 700L.
Generally, multifunction machines are not suitable for large outer diameters or long lengths. However, we have experience with the above sizes, so we can say that our processing range is quite wide. However, it is not possible depending on the shape of the workpiece, so please contact us first.
- I need composite processing. Can you do it in small quantities?
-
Yes, we can handle a wide variety of products and small quantities.
Other companies charge too much for a large variety! They don’t accept small quantities! We can solve your problems. Please contact us for more information.
- I need an inspection sheet.
-
Yes.
Please note, however, that an additional charge may be incurred depending on the contents of the order, such as the specified paper and the number of specified sections.
Contact us
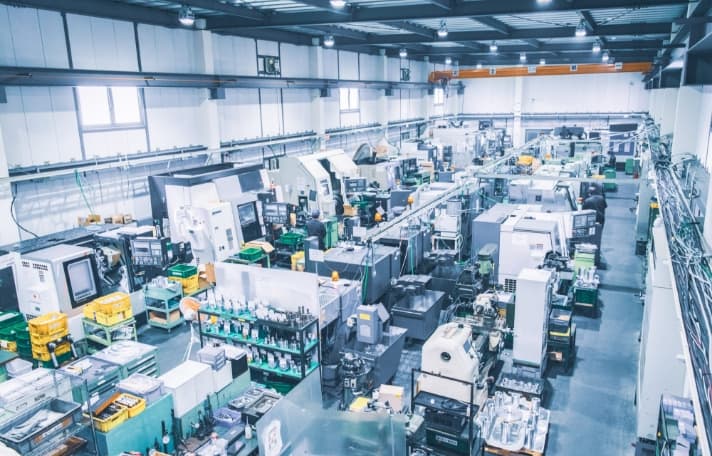
Morii Presents You World Class Aluminum Processing Technology for OPTICAL SYSTEM and MEDICAL Parts.
- Thin-walled Precision Aluminum Processing
- SUS and Difficult-to-cut Titanium Material Processing
Please email me anytime if you have any question.
5-1-15 Wakaehigashi,Higashi Osaka,Osaka,Japan
578-0935
E-mail: morii-mfg@moriiss.co.jp